Microsilica Manufacture Iranian Suppliers Available in Jumbo Bag In Best Price
- Iran's microsilica has international standards, including Iran 13278, ASTM C 1240, EN 13263 and JIS A 6207.
- In concrete, depending on the application, it varies between 7 and 15% of cement weight.
- It is an environmentally friendly product that is packaged in 40 kg bag sizes up to 750 kg bulk.
- Proper use of lubricant or water reducer has a high range, the air absorption rate is 1.5 to 2 times higher than normal concrete.
- Handling precautions include avoiding inhalation, eye and skin contact, and exposure to hydrofluoric acid, with a risk of forming harmful particles when heated above 1000°C.
Iran's Microsilica: Standards, Usage, Packaging, and Safety Precautions
Microsilica Iranian Suppliers According to ACI 116R code, Iranian micro-silica consists of very fine amorphous silica particles that are electrically produced as a by-product of silicon alloy or ferrosilicon production. Physically, chemically, and in terms of application, it is different from micronized crystalline silica obtained from silica rock mills. It has two names: Micro Silica and Silica fume. Microsilica of Iran is prepared for use in concrete, mortar and slurry by following the special and suitable instructions for use following the international technical standards determined by the Road, Housing and Urban Development Research Center of Iran.
Iran's microsilica complies with Iran national standard 13278 and complies with ASTM C 1240, European EN 13263 and Japanese JIS A 6207 standards.
65% of global micro silica production is used in cement and concrete industries. Its used include blended cement production, high strength concrete (HSC), High Performance concrete (HPC), Self-consolidating concrete (SCC), shotcrete, low permeability concrete, repair concrete, and fiber-reinforced polymer (FRP).
Recommended dosage of Microsilica in concrete mixed varies depending on the application, typically ranging from 7% to 15% by weight of cement.
Advantage of Microsilica
It’s using in the cement and concrete include initial compressive strength enhancement, reduced water and chloride ion permeability, increased durability, modulus of elasticity enhancement, improved flexural strength, increased hardness, improved adhesion, reduced shrinkage, increased abrasion resistance in pavements, floors, overlays, and spillways of dams, and enhanced resistance to alkali-silica reaction (ASR).
Economic information
including the reduction of life cycle costs due to fewer repair cycles, savings in the construction of concrete structures, enabling thinner elements, In bridge construction, by increasing span life, reducing shotcrete costs by minimizing return material, and reducing floor construction by allowing one-time payment.
Environmentally Effect
Microsilica is an environmentally: friendly by-product in Iran and does not raise environmental issues related to cement.
Use of microsilica in the project
Important projects using microsilica include the Milad Telecommunication Tower in Tehran, desalination facilities in Bandar Abbas, water reservoirs in the Asalouye region, Ahvaz city train and Qom monorail.
Microsilica is packaged size
Iran microsilica in large bags (750 kg), medium bags (500 kg), small bags (40 kg), and bulk (bunker).
Storage conditions:
Microsilica in bags is the same as Portland cement, plus the silo inlet pipe for bulk microsilica must be plastic. Microsilica does not hydrate in the presence of moisture, but can agglomerate and requires grinding before use. In agglomerated form, microsilica acts as a filler.
When mixing microsilica with other components of concrete, it should not be added to the mixer before the other ingredients. The mixer should be filled up to 63% of its nominal capacity.
Application Method Microsilica should be used with a high-range lubricant or water reducer. The percentage of air absorption should be 1.5 to 2 times higher than the percentage used for ordinary concrete.
There is minimal or no water leakage from concrete containing microsilica, allowing for faster curing, although the risk of plastic shrinkage cracking is greater compared to conventional concrete. Proper management can reduce or mitigate this risk.
Concrete pouring and curing methods for microsilica are similar to conventional concrete methods. It is recommended to start finishing operations 10-15 minutes after pouring.
Health and safety
precautions include avoiding inhalation and direct contact with eyes and skin and avoiding exposure to hydrofluoric acid (HF). Heating above 1000°C can lead to the formation of cristobalite/tridymite crystalline particles.
Due to the content of more than 99.5% amorphous particles, microsilica does not cause silicosis or respiratory discomfort.
Customer reviews
Add your review
Your email address will not be published. Required fields are marked *
Please login to write review!
2 review(s) for "Microsilica Manufacture Iranian Suppliers Available in Jumbo Bag In Best Price"
by Abrisham Road
Inspection group .co
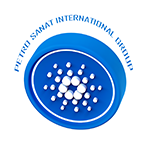
Petro Sanat International Group
- Store rating
5
- Staff
15
- Offers
> 100
- Products
4